We measure the strength of cured concrete by testing the pounds force per square inch or psi. The psi rating refers to the compressive strength of the concrete or its resistance to a downward force.
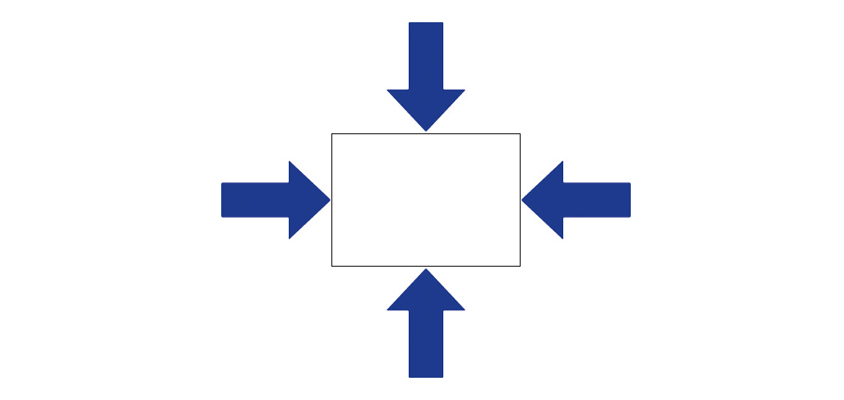
Psi of concrete refers to its compression strength.
While the compressive strength of concrete is excellent, it lacks tensile strength or the ability to resist flexing. In other words concrete is brittle. Concrete tested to 4,000 psi of compressive strength would typically have a tensile strength of only 10% or 400 psi.
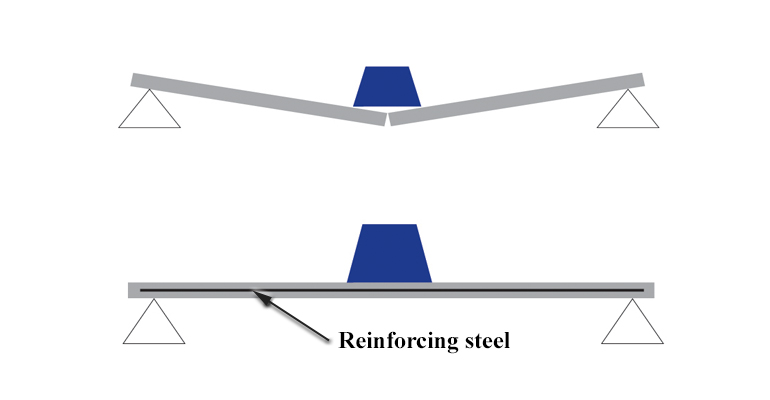
Steel possesses excellent tensile strength.
Steel possesses the opposite characteristic of concrete with high tensile strength. These opposing properties are why the two materials are used together when producing concrete products. Embedding reinforcing steel in the concrete increases its ability to resist failure from tensile stress.
Concrete slats are cast with steel bars placed at the top and bottom of the slats. The top bars protect the slat from cracking while the slat is being transported and set in place. After the slat is in place, the lower bar keeps the slat from cracking on the bottom.
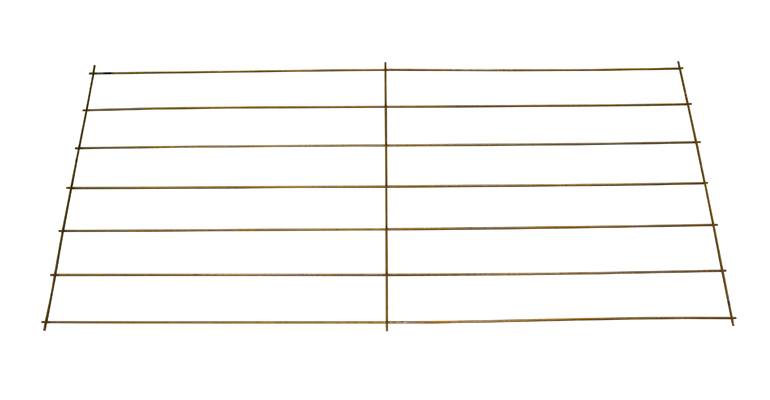
Welded Wire Mats have several advantages over rebar for slat production.
While rebar is the most common type of reinforcing steel used in poured-in-place concrete, welded wire reinforcement mats offer some distinct advantages when used in the production of concrete slats. Fabrication of WWR mats consists of welding steel rods into large sheets specific to each slat mold.
- WWR mats are made from high tensile 80,000-psi steel wire formed by special equipment to the proper diameter and straightened. In comparison, rebar has a lower 60,000-psi rating.
- By welding them into a mat, the rods do not move when concrete is placed, ensuring each bar is in its proper position.
- Automated equipment located in a controlled environment prefabricates the WWR mats lowering the risk of improper welds that can affect the strength of the steel.
In general, using Welded Wire Reinforcement mats in the manufacturing of precast concrete slats yields a much more consistent product than production using individually placed rebar.