Unlike a sponge, concrete does not reabsorb water after it dries. The water doesn’t leave the mixture; it reacts with it and becomes part of the final form of the concrete.
Instead of drying, concrete instead cures. The water added to the mixture reacts or hydrates with the cement and aggregates to form the bond that creates concrete. Concrete does not need to dry out to harden as is commonly thought. In fact the mixture needs to have moisture present to set correctly.
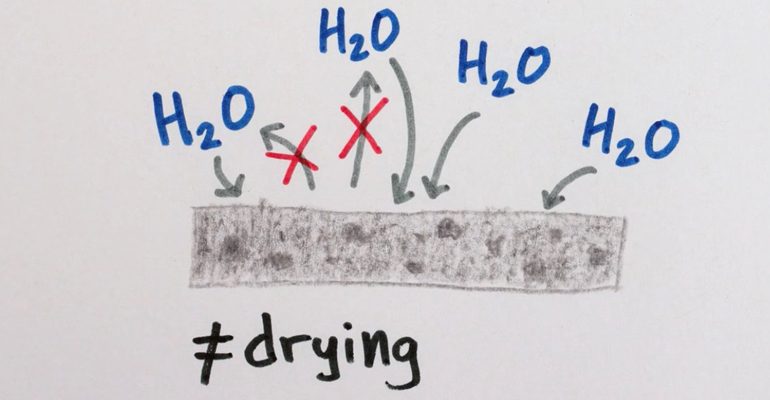
Water reacts with and becomes part of the final form of the concrete.
The most common and low-tech method to cure precast concrete is to allow it to “set up” at the existing ambient temperature for a period longer than 28 days. Problems with this process occur when the temperatures are too low, or it is necessary to ship product before 28 days.
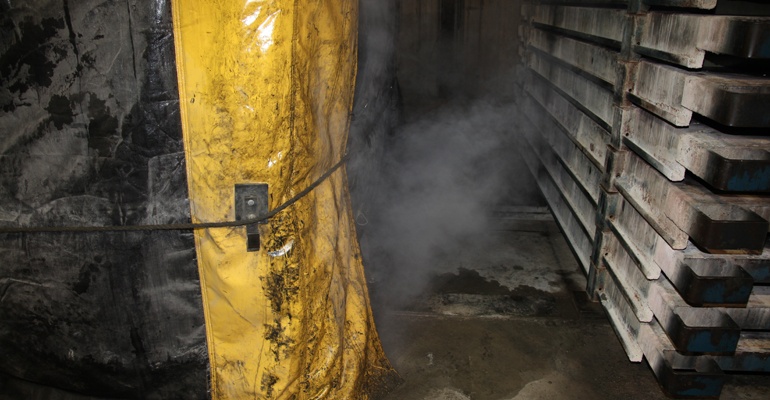
Accelerated curing using steam produces a more consistent quality of precast concrete.
Accelerated curing using steam produces a more consistent quality of precast concrete. The slats are stacked and covered with a tent with steam pumped into the enclosures. The increased heat of the steam speeds up the cure time and provides additional moisture so the water inside the concrete is not lost and can complete the hydration process. The strength of steam heat concrete after three days will equal or exceed the 28-day strength of normally cured concrete.
This method of curing slats provides several advantages.
First, the curing process isn’t affected by the weather. Cold, heat, wet, and dry conditions don’t change the final strength of the slats and beams.
Second, faster cure time permits slats to be shipped to a job site without a standard 28-day cure time. This reduced time is especially critical during the height of the building season when slats might be in short supply. Slat manufacturers using an air cure method might be tempted to cut corners and ship slats before they are ready.
The proper curing of concrete slats determines its quality and projected life cycle in production facilities. Controlled curing with steam heat provides all the elements needed for manufacturing consistently high-quality products.